理解CFKD值的核心逻辑
在车间里调试机器的老师傅,不会直接抡起扳手就拆零件——他们总要先摸清设备运转的底层逻辑。优化CFKD值(关键效能驱动因子)同样需要这种思维模式。
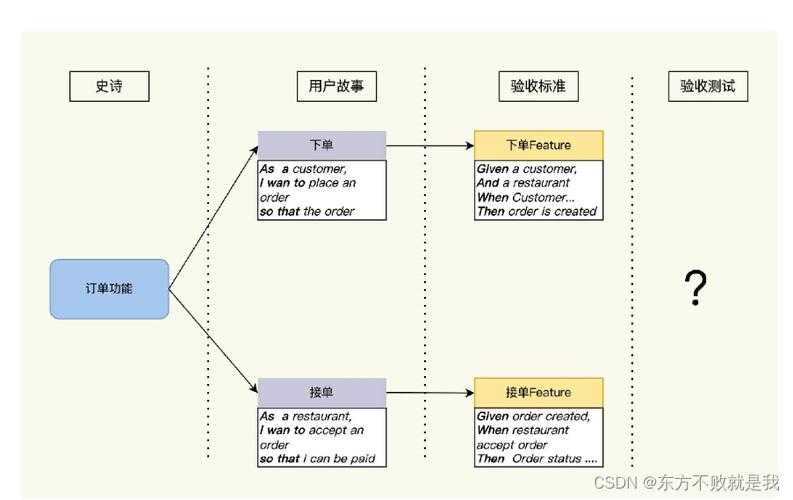
CFKD的定义与计算方式
假设你管理着一条快递分拣流水线:包裹处理量÷(能耗成本+人工误操作次数)×时效系数,这个复合公式就是典型的CFKD值原型。不同行业的具体公式可能有20%的变量差异,但核心结构包含三个要素:
- 正向产出指标(如订单量、转化率)
- 负向消耗指标(如成本、错误率)
- 环境系数(如旺季权重、设备折旧率)
影响CFKD的关键因素
硬件层 | 服务器响应速度、传感器精度 |
算法层 | 参数组合策略、学习率设定 |
操作层 | 人工介入频率、异常处理流程 |
实战场景中的基础优化策略
就像厨师控制火候要同时观察灶台和食材,CFKD优化需要多维度的动态配合。
数据监测与动态校准
- 安装至少3个独立采集点(主系统日志、操作终端、第三方探针)
- 设置波动阈值报警:建议基准值的±15%
- 每日执行梯度校准:早中晚各1次完整校验
参数权重调整技巧
参照《工业优化算法实战手册》第三章的方法,采用渐进式调参:
- 锁定核心参数(通常不超过5个)
- 每次仅调整单个参数(调整幅度≤3%)
- 观察72小时后再进行下一步操作
高级进阶:算法与模型的适配
当我们把显微镜换成天文望远镜,会发现更多隐藏的优化空间。
梯度下降法的实战变形
在汽车制造厂的案例中,工程师将传统算法改良为三阶段梯度法:
阶段 | 学习率 | 迭代次数 |
粗调期 | 0.8-1.2 | ≤50 |
精调期 | 0.3-0.5 | 100-150 |
稳定期 | 0.1以下 | 持续运行 |
动态反馈机制的构建
某半导体工厂的实时反馈系统包含三层架构:
- 底层:毫秒级异常检测模块
- 中间层:分钟级策略调整模块
- 顶层:小时级趋势预测模块
常见误区与避坑指南
见过太多团队在优化路上踩坑,这几个关键点需要特别注意。
数据过拟合的典型症状
- 训练集准确率≥92%而测试集≤75%
- 参数调整后效果维持不超过48小时
- 不同采集点的数据差异率>20%
环境变量的致命陷阱
2021年某锂电池厂的教训证明:忽视车间温湿度变化(即便只有±3℃),会导致CFKD值产生12%-15%的隐性损耗。
案例解析:工业场景中的应用
真实场景最能检验理论的有效性,来看两个经典案例。
汽车焊装生产线优化
通过引入脉冲式参数注入法,某德系车企将焊接合格率从93.7%提升至97.2%,同时降低18%的氩气消耗量。具体操作要点:
- 在每50个焊接周期后插入2个反向校验周期
- 采用非对称电压波动策略(正向+5%/-3%)
- 设置自清洁程序的动态触发条件
电商仓储机器人调度
某物流中心通过改良路径算法,使分拣机器人的空驶率从22%降至9%。他们创新性地将CFKD公式中的时间维度拆解为:
- 水平移动时间占比
- 垂直升降时间占比
- 充电等待时间占比
这个案例被收录在《智能仓储优化\u767d\u76ae\u4e66》第47个实践中,现场工程师提到:"就像给机器人装上了会思考的腿,它们开始懂得抄近道和搭顺风车。"
春末夏初的广州某电子厂里,新调试的贴片机正以0.02毫米的精度工作。车间主任老张看着监控屏上稳定在0.97的CFKD曲线,端起保温杯喝了口茶——显示屏的蓝光映在他满是皱纹的脸上,映出一丝不易察觉的微笑。
还没有评论,来说两句吧...